Product quality
Meeting the needs of our customers takes more than only the development of an FIBC (Big Bag). Quality considerations always play an integral part during all processes. Starting with the selection of materials, through to the adoption of latest technology and the maintenance of strict safety standards to the punctual on-time delivery of the finished product - all stages in the development and supply of a Technopac product, with which our customers can be fully satisfied, rank of equal importance.
Quality standards - certified partners
Quality standards are used to ensure the system works smoothly and the final product meets the desired criteria. A quality management system such as ISO 9001 prescribes certain procedures which are required to achieve this standard. All manufacturing partners of Technopac are certified according to the current ISO 9002 standard. This certification confirms compliance with the required standards in areas of production, organisation and documentation. Given the increasing demands for higher quality and better service, Production went a step further and in the last quarter of 2003, obtained certification ISO 9001-2000, ISO 14001 and the updated certification ISO 9001: 2000. We are constantly working to improve the quality.
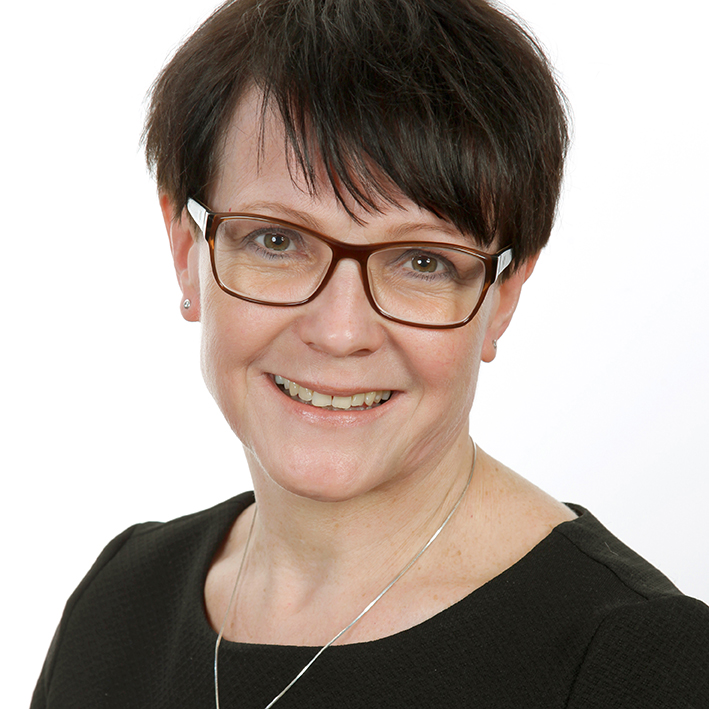
Get in touch with me,
I will help you!
Bettina Rauchberger
Sales Account Manager | ||
Tel.: +43 2746 330 60-13 | ||
For external testing, inspection and certification of our products we rely on the experts of OFI
- Dipl.-Ing. Rudolf BAUMGARTNER, MSc for the transport of dangerous goods
- Dr. Michael WASHÜTTL for Food & Packaging
At OFI, you get everything from a single source - personal advice, innovative solutions and security with guarantee.
Being an accredited testing, inspection and certification body - accredited and approved by Accreditation Austria / bmwfw - the quality of OFIs work is also guaranteed by the state.
Quality - highest priority
Quality has the highest priority at Technopac. Our manufacturing partner has a well-equipped laboratory and internal quality assurance which includes a test rig for big bags.
The quality assurance process consists of three stages:
- Material inspection and testing
- production monitoring and control
- Final quality control
For material control the tapes are tested for width and strength. Once the yarns are woven, the fabric is checked again for width, weight and fabric density and strength of the warp and weft threads. Fabric samples are also tested for UV resistance. A further careful control process is carried out in the final quality control stage. The bags are measured and subjected to a visual inspection to ensure that customer specifications are fully met. Finally, a strength test is carried out using a simulated test to destruction.
Test parameters
stretch test
tensile
UV resistance test
coating adhesion test
sift proof properties test
Cyclic Lifting and destruction test
elevation Test
Topple test
Drop Test
Stacking test
Fabric examination
Friction test
These tests and final checks are all performed on the bag during the final quality control process.
Traceability
In the unlikely event of a manufacturing fault our manufacturing partners are able to determine the root cause of the problem by having complete traceability through all stages of production back to the raw material used. With this system of quality assurance and traceability in place, any non-conforming products can readily be identified at the production stage. Any non-conforming products are immediately removed from the process whilst necessary steps taken to resolve the problem before goods leave the factory.
Ensuring we have in place a consistent, robust quality assurance system ensures that we are able to deliver products to our customers which they can rely and trust upon.